X-EL Energy Management
Electrification and Hybrid Solutions
Electrification and hybrid power technologies offer exceptional optimisation potential for today’s vessels, helping to improve fuel efficiency and reduce emissions while improving reliability and load response across the integrated power system.
WinGD takes a holistic approach to designing power arrangements that go far beyond the main engine. By incorporating and configuring electric hybrid technologies to suit your vessel characteristics and operating profile - alongside our proprietary energy management system to keep you operating at optimal efficiency – WinGD can ensure vessels built or retrofitted today are prepared to face operational and regulatory challenges across their lifetime.
System Topology: Optimally sized components, fulfilling technical and commercial requirements |
Control Strategy: Energy management system, aiming for maximum efficiency of the ship as a whole |
Lifecycle management: An integrated advisory system for operation, diagnostics and maintenance |
System topology
Hybrid technologies that can help improve efficiency and reduce reliance on fossil fuels include shaft or front-end generators, batteries, power converters, and when required, shore power interfaces, solar/wind power generation and fuel cells.
As one example of a hybrid arrangement, a shaft or free-end generator driven by the two-stroke main engine can deliver electrical power that can be used for either propulsion or auxiliary demand, reducing fuel consumption and emissions – at the same time improving EEXI, EEDI and CII performance. The solutions also reduce maintenance spend on auxiliary engines onboard due to lower running hours during the voyage.
Generator arrangements can be installed on either single- or twin-screw applications and consist of shaft generator(s) and a variable frequency converter. Where required, a transformer is applied as an interface between the converter and the ship’s AC power grid.
WinGD has developed a flexible process for deploying hybrid power solutions, using its extensive engine experience to optimally integrate the prime mover and electric power sources. This includes selecting appropriate technologies and, crucially, the sizing of all system components. These system integration capabilities ensure that ship operators’ chosen solutions – including main engine and electric power sources - are part of an optimised, fit-for-purpose, holistic energy system.
Control strategy
Hybrid power arrangements integrated by WinGD are all governed by the state-of-the-art WinGD Hybrid Control System.
Validation and tuning of these controls can take place at an early stage in development thanks to WinGD’s simulation and development toolchain. These enable customers to assess the build and operation of the power arrangement in digital form, simplifying the physical integration, commissioning and testing of the systems.
The controls aim to deliver maximum ship efficiency at any given moment. A well-managed energy system delivers intelligently optimised power production at any moment, weighing a range of factors including cargo load, ship speed, environmental conditions and route. The hybrid solutions are applicable on both – fixed- and controllable pitch propellers.
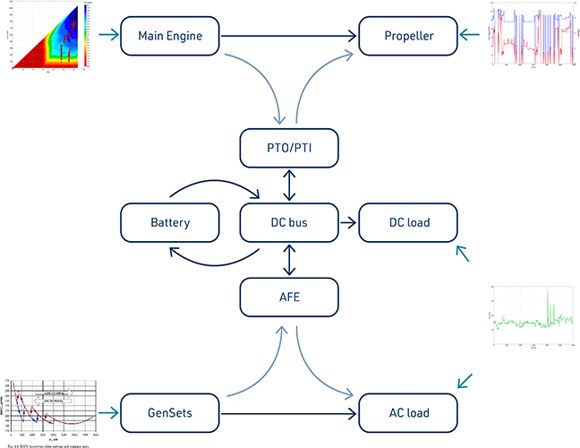
Lifecycle management
WinGD’s virtual development toolchain provide the basis for the system’s digital twin, which enables benchmarking of system behaviour in service, leading to further efficiency improvements by optimising control strategies depending on real operating conditions. The digital twin also informs the integrated advisory system designed to assist ship operators with optimising power system operation, diagnostics and maintenance.
The lifecycle benefits of an optimally integrated holistic energy system go deeper than intelligent control and advisory. Integration leads to efficient utilisation across all energy resources, including maximising use of the main engine, increasing propeller efficiency through power take-out and minimising (or even eliminating) the use of less efficient auxiliary engines. Transient behaviour of machinery is also improved as the system can respond quicker to load changes than a single power source prime mover.